As the popularity of new energy vehicles continues to rise, the market demand for Advanced Driver Assistance Systems (ADAS) has surged. Consequently, in recent years, the number of LiDARs (Light Detection and Ranging) installed in vehicles has been growing rapidly, especially in China, where electric vehicles are ubiquitous from north to south, and an increasing number of cars are equipped with LiDARs.
In 2023, the global passenger car LiDAR shipment volume exceeded 500,000 units, and the shipment volume for 2024 is expected to reach 1 million units. This 1 million figure corresponds to a market penetration rate of around 1%, indicating that there is still significant room for growth.
Since 2021, automakers such as XPeng, NIO, Li Auto, Arcfox, and IM Motors have begun to gradually introduce models equipped with LiDARs, with the number of LiDARs per vehicle ranging from 1 to 4. More and more manufacturers are also planning to incorporate LiDARs into their vehicles. According to Yole, as of the third quarter of 2023, 36 Chinese automakers have announced the use of LiDARs, with approximately 106 models equipped with LiDARs launched in China, accounting for 90% of the total number of new models worldwide equipped with LiDARs during the same period.
Advertisement
01
A Brief Analysis of Automotive LiDARs
ADAS can be divided into 5 levels, from L1 to L5, with the degree of driving automation gradually increasing. Correspondingly, the variety and number of sensors are also increasing. From the industry's understanding of ADAS systems in previous years, L4 definitely requires LiDAR, while at the L3 stage, many companies still do not use LiDAR because of its high cost.
LiDAR can generate a 3D view of the road by measuring the time it takes for light to travel to an object and reflect back, providing a 3D point cloud map of the car's surrounding environment, which helps the car to accurately recognize its surroundings. Despite differing opinions in the ADAS industry regarding LiDAR, it is generally considered one of the core sensing technologies for ADAS due to its ability to create high-definition 3D point cloud maps of the surrounding environment.
LiDARs are mainly divided into mechanical, semi-solid-state, and solid-state types.Mechanical LiDARs face challenges in assembly and have low scanning frequencies; semi-solid-state solutions feature decoupling of the transceiver unit from the scanning component, with the transceiver unit (such as lasers and detectors) no longer undergoing mechanical motion, suitable for partial field-of-view detection (e.g., forward-facing), and more compact in volume compared to mechanical radars; solid-state LiDARs mainly include scanning methods like MEMS, Flash, and optical phased array (OPA).
The emission modules of LiDARs primarily employ two detection methods: the mainstream is ToF (Time of Flight), and the emerging one is FMCW (Frequency Modulated Continuous Wave). The mainstream laser for emitting lasers is EEL (Edge Emitting Laser), with VCSEL (Vertical Cavity Surface Emitting Laser) as an emerging option.
In the reception module, the mainstream detection technology is APD (Avalanche Photodiode), with SPAD (Single-Photon Avalanche Diode) and SiPM (Silicon Photomultiplier) as emerging technologies. APD is an avalanche photodiode, which has the disadvantages of large size, high power consumption, limited detection distance and range, and poor consistency. Adopting the SPAD solution can significantly reduce costs, with smaller size and more stable performance. SiPM is a silicon photomultiplier, with advantages such as a gain 10,000 times that of APD, a sensitivity 2,000 times that of APD, and very low operating voltage requirements, only 30V compared to 250V for APD. SiPM has excellent consistency, making it easier to achieve mass production.
02
Market Landscape
Globally, the main players in the LiDAR industry include Velodyne, Luminar, Aeva, Ouster from the United States, Innoviz from Israel, and from China, companies like RoboSense, Hesai Technology, TuSimple, and Huawei. In the early years, during the initial stages of industry development, foreign companies like those in the United States dominated the technology and product markets. In recent years, with the rapid development of China's new energy vehicle industry, domestic LiDAR companies have invested significant resources and funds in research and development, gradually catching up technologically and even surpassing in certain areas, with their market share of related products also rapidly expanding.
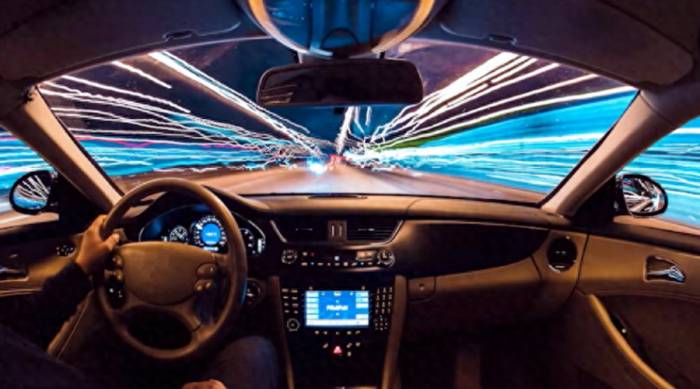
In 2022, Hesai secured the top position in global automotive LiDAR revenue for two consecutive years with nearly 50% market share, expanding from 42% in 2021 to 47%. TuSimple, relying on continuous shipments from NIO, captured the second place with a 15% market share, while Valeo and RoboSense ranked third and fourth with 13% and 9% market shares, respectively.
According to Yole's statistics, in 2023, among the top five global automotive LiDAR market share manufacturers, the top three are all Chinese companies, namely Hesai, RoboSense, and TuSimple, with a combined market share of 80%. The remaining 20% market share is divided among companies such as Valeo, DJI Livox, Huawei, Cepton, and Innoviz.Behind the Scenery Lies High Costs and Losses
Currently, automotive LiDAR is still in the middle and early stages of development, with performance and cost being the challenges that the industry is striving to overcome. Particularly concerning cost, the price of each LiDAR unit currently ranges from $1,000 to $3,000. If we include some auxiliary materials, then the expenditure for car manufacturers on LiDAR alone can reach up to $10,000. Therefore, the prices of models on the market that use LiDAR are mostly around 300,000 yuan.
In the face of high costs, although the market appears to be booming and the products of major manufacturers are selling well, their profitability is not optimistic.
Taking Hesai and RoboSense as examples, in 2022, Hesai's revenue was 1.203 billion yuan, a year-on-year increase of 66.86%. The cumulative annual shipment of LiDAR exceeded 80,400 units, with a record increase of 467.5%. Their revenue and delivery volume exceeded the total of eight international peers. However, Hesai's net loss also expanded by 22.85% compared to the previous year, reaching 301 million yuan, and the gross margin dropped from 70% in 2019 to 39%.
In the second quarter of 2023, Hesai's revenue increased by 108.5% to 440 million yuan, with a year-on-year increase in delivery volume of up to 946.5%, reaching 52,100 units. The net loss narrowed by 37.4%. In the first half of 2023, Hesai's delivery volume exceeded the entire year of 2022, but the gross margin fell to a historical low of 29.8%.
RoboSense's prospectus shows that from 2020 to 2022, the company sold 300, 4,000, and 36,900 ADAS LiDAR units, with corresponding revenues of 61.75 million yuan, 400.89 million yuan, and 160 million yuan, respectively. Despite the continuous increase in shipments, profits are meager. The average selling price of a single LiDAR unit dropped from 20,500 yuan to 4,346 yuan. From 2020 to 2022, the company's adjusted net losses were 59.93 million yuan, 108 million yuan, and 563 million yuan, respectively. The gross margin was 44.1% in 2020, 42.4% in 2021, and declined to -7.4% in 2022.
In other words, RoboSense has adopted a strategy of trading price for volume, preferring to incur losses in the medium and short term to ensure sufficient shipments. As of March 2023, RoboSense has secured pre-installation orders for 52 models from 21 car manufacturers, ranking first globally.
Both RoboSense and Hesai exemplify the awkward situation of LiDAR manufacturers in recent years, where they trade price for volume, increasing revenue but not profits.For Chinese automotive manufacturers, due to the exceptionally fierce competition and the sluggish overall economic situation, reducing costs has become the only choice, a situation that is not friendly to LiDAR technology.
In 2023, many car companies have gradually shifted from using high-precision maps as a selling point for advanced intelligent driving to emphasizing a light map mode led by BEV+Transformer.
Looking at some recently launched products, except for ultra-high-end models, other products are almost all reducing the use of LiDAR. Currently, single LiDAR and dual LiDAR are gradually becoming the industry mainstream. Huawei, Li Auto, and NIO are using single LiDAR solutions, while XPeng and Great Wall's Blue Mountain are using dual LiDAR solutions. Multi-LiDAR solutions with three or more have basically disappeared.
To solve the cost issue, various companies, especially chip manufacturers, are leveraging their strengths in the three technological paths of solid-state LiDAR, all hoping to lower the price to a few hundred US dollars, or even below 100 US dollars.
04
International giants under great pressure
With such a high market share of local LiDAR companies in China, their profitability is still so bleak, and the situation for international giants with lower market shares is even worse.
Although there is not much profit, the aforementioned local Chinese companies are still increasing their shipment volumes. At the beginning of 2024, several leading Chinese manufacturers issued reports, with both monthly and annual delivery volumes reaching new highs.
Hesai Technology announced that the number of LiDAR deliveries in December 2023 exceeded 50,000, surpassing the previous guidance of 220,000 for the whole year of 2023; RoboSense officially announced that in December 2023, the monthly sales of LiDAR broke through 70,000, and in the fourth quarter of 2023, sales reached 151,000 units, a year-on-year increase of 545.30%, exceeding the total of the first three quarters; TuSimple announced that the delivery volume of automotive LiDAR in 2023 exceeded 150,000 units, with a growth rate of over 100%.Based on the sales data disclosed by these leading manufacturers, in the year 2023, the sales volume of Chinese lidar exceeded 600,000 units.
As a result, overseas major manufacturers had to retract their automotive lidar front lines.
In September 2023, Bosch, which had been investing in lidar research and development for nearly three years, suddenly announced the abandonment of self-developed lidar.
Ouster's revenue in the second quarter of 2023 exceeded $19 million, a year-on-year increase of 88%. However, the gross margin was only 1%, compared to a gross margin of 27% in the second quarter of 2022. This was mainly due to the significant negative impact on the company's profits after the merger of Ouster and Velodyne, resulting in a net loss of $123 million for the quarter.
Luminar's revenue in the first half of 2023 increased by more than $30 million, a year-on-year increase of 83%, but it is still in a loss-making state. The loss in the second quarter of the previous year was about $140 million, and the loss expanded by 49% year-on-year. In order to reverse the unfavorable situation, Luminar carried out a comprehensive optimization and process verification at its automated factory in Mexico, striving to meet the requirements of downstream vehicle manufacturers. At the same time, it announced a cooperation with TPK to establish a factory in Asia.
In early May, Luminar announced that it would lay off 20% of its workforce.
Luminar's founder and CEO, Austin Russell, stated in an open letter that despite the company's core business in technology, products, industrialization, and commercialization being stronger than ever, Luminar is facing unprecedented challenges in the capital market. To date, the company has invested $1.8 billion to establish a breakthrough technological foundation starting from the semiconductor level and has successfully launched the SOP standard technology. However, the current business model and cost structure are no longer suitable for the company's needs.
The 20% workforce reduction is to reduce costs, as part of the restructuring, Luminar will also flatten the organizational structure and achieve financial flexibility; it also seeks to sublet part or all of its facilities to reduce the size of the enterprise.
The company stated that the plan will be implemented immediately, and after completion by the end of 2024, the annual operating costs will be reduced by $50 to $65 million. It is expected that within the next five years, more than $400 million in cost savings will be achieved.The Challenge of Pure Vision Solutions
In previous years, it was widely believed in the industry that for ADAS systems at Level 3 and above, the use of LiDAR was essential to ensure system functionality and safety. However, developments over the past two years suggest a shift in this perception, with Tesla being the primary disruptor in the market.
For many years, Tesla has been skeptical about LiDAR, insisting on a pure vision approach. Judging by the company's continuously accumulating data and the iterative improvements in AI capabilities and performance, it seems possible to achieve ADAS at Level 3 and above without LiDAR. This is clearly bearish for the LiDAR market and related enterprises, potentially exacerbating the profitability challenges faced by major LiDAR manufacturers.
Currently, in-vehicle camera solutions are primarily divided into vision-centric and multi-sensor fusion approaches.
The vision-centric solution, led by cameras, demands high algorithmic requirements. Tesla excels in this area; its entire fleet equipped with the Autopilot 3.0 system does not use LiDAR. Instead, it employs eight cameras, one millimeter-wave radar, and twelve ultrasonic sensors. These include three forward-facing, four side-facing, and one rear-facing camera, providing a 360-degree view within a 250-meter radius for the vehicle.
The multi-sensor fusion approach emphasizes the importance of the hardware system and has relatively lower algorithmic demands. The sensor count for such solutions is continuously increasing, with more intelligent vehicles using over ten cameras. The CIS (CMOS Image Sensor) resolution is also high; for example, the NIO ET7 uses eleven 8-megapixel high-definition cameras, and the Zeekr 001 utilizes fourteen cameras, including seven 8-megapixel high-definition cameras.
At present, the most widely used sensors in ADAS are CIS image sensors, which also offer the best cost-performance ratio. Infrared sensors are indispensable at night, and ultrasonic radars are necessary for parking. These are the essential sensors for current ADAS systems. With the evolution of application needs, millimeter-wave radars are also increasingly appearing in vehicles. However, due to their high cost, there is still debate over the application of these sensors. Intelligent electric vehicles, represented by Tesla, have not adopted them, relying mainly on CIS and Tesla's powerful algorithmic capabilities to achieve ADAS.
Elon Musk believes that the pure vision approach has significant advantages. Because it aligns with the natural human driving perception through vision, the system can directly recognize information from anything that the "eyes" (cameras) can see, making accurate judgments. This is considered more reliable than abstract data collected by sensors. Coupled with well-developed high-precision maps, it can achieve a high level of ADAS functionality.
Even high-end cameras cost only a few tens of dollars. From this perspective, to meet the functionality of assisted driving, the cost of the pure vision solution is much more attractive compared to LiDAR.Of course, pure vision solutions also have drawbacks. For instance, relying solely on visual information cannot achieve more sophisticated 3D modeling, which means that in terms of depth perception, pure vision solutions struggle to reach a higher level. In response to this, Tesla's strategy is to utilize artificial intelligence and more advanced software algorithms to address the issue.
06
Conclusion
Faced with high costs and competition from pure vision solutions, lidar companies must optimize both cost and technology to ensure long-term development in the future.
How can costs be further reduced? This can be achieved by optimizing the design, including the development of proprietary lidar chips and SoC integration, to enhance system integration.
Although each lidar manufacturer has its own development path, costs are largely concentrated in the transmitter-receiver and sensor chips, accounting for about 50% to 70% of the total cost. Therefore, increasing the integration of related modules is considered the preferred solution for reducing lidar costs. Taking the transmitter chip as an example, replacing discrete modules with integrated modules can reduce material and calibration costs by more than 70%.
By developing their own transceiver chips, lidar manufacturers can expand their profit margins. At the same time, adopting modular design can effectively shorten production calibration time, simplify the process, achieve higher yield rates, promote large-scale production, and thus reduce costs.
Comment